|

05-14-2018, 03:56 PM
|
 |
Member
|
|
Join Date: Oct 2011
Location: Roseburg, OR
Posts: 86
Thanks: 0
Thanked 32 Times in 17 Posts
|
|
72 Nova - C5 Corvette Suspension Swap Project!
This is a relocation of my "Introduction" thread... which I'll delete when the move is complete. I also updated it a little bit, since I'm no longer 24 like I was when I started this thread! It's always kind of fun to go through the thread, as I can see how this car has been with me through so much of life... from highschool, Prom night, college... now I'm married and have a toddler!
I Joined this site due to a recommendation from Robert at Automotive Design Engineering... so far I think he made a good recommendation! This site has alot of good, technical information and real build threads.
Anyway, I'm 31 now, I work as a mechanical engineer at a company that makes castings for jet engines and such, based in Portland Oregon. I became an engineer as I've always loved working with my hands on mechanical devices, largely due to my experiences working on my nova as a teenager.
About [s]four[/s] 11 years ago, I happened across a corvette chassis/engine/transaxle drop-out on eBay... and that got the gears going in my head.
Pretty much since that day, I've been planning this project. Saving money... not to buy the parts, but to buy a house with a good sized shop. With the house found, I finished out the shop, and got ready for this project.
Anyway, I've owned this car since I was 15, in 2003, when it looked like this:
I painted it before I turned 16. Did all the body work, panel replacement, primer, and final paint. Had a professional help me mask the racing stripes. I was such a fresh faced young man for my first prom!
As high school came to an end, and college began, the poor old nova began to see neglect. I couldn't afford to drive it, so it got parked, and the motor was eventually pulled and used in a circle track car. And there it sat.
As the car sat, covered in dust... I looked at corvette chassis on eBay, thought about wheel choices, engine combos. All the while saving, saving saving. I needed a place to do this project. And eventually, the perfect piece of property came along. It had a 32x24 shop. It was also cheap, well located. minutes from work, minutes from downtown Portland, and it also had some kind of house or something, which turned out to be pretty nice as well.
After re-wiring the house and shop, and getting my quarterly bonus and huge tax return, I was finally financially and schedule ready to begin this project. First step, dragging the old nova out of the hay barn in Roseburg Oregon up to Portland. My dad and brother get big props here for hauling the car up for me. Even after sitting all that time, it cleaned up nice!
March 2011
Next step: Frame jigg. This thing is square to within 1/32 of an inch, and flat to within .005" per foot. I thought having the beams right under track width of the car would be a good idea. After building it, I realized this was not the case, since I can't install a wheel and tire on the rear-end without getting them caught in the wheel well. lesson for next time is to make it a bit narrower or wider.
Last edited by nickcornilsen; 11-10-2020 at 06:04 PM.
|

05-14-2018, 03:58 PM
|
 |
Member
|
|
Join Date: Oct 2011
Location: Roseburg, OR
Posts: 86
Thanks: 0
Thanked 32 Times in 17 Posts
|
|
April 2011
So then work began on tearing the car down. The old 9" axle and front sub frame had to go. I was able to recoup a bit of coin by selling these, which was nice.
I threw one of the 295 rear tires under the front, just for kicks.
In order to design this thing, I needed the tires and wheels, so I could figure out the track width. So i spent $1200 on tires and wheels! Aint no thang. Fronts are 265 35 17s, the rears are 315 30 18's. I also bought the corvette front and rear suspension drop-outs, and transmission.
And with that, I began the design. All CAD'd so I could have pieces cut on a water jet.
I needed to narrow the track width about 3 inches... the only steering rack that was close to the right width was from a 93-02 camaro. It is 4 inches narrower than a C5, but mounts differently.
After finishing the design, I had the parts cut out on a water-jet.
At this point, I needed to build my jig. I had all of the pieces cut out so they had a "datum" tab that was on a plane 5" above the simulated ground. i needed to build the rails for that to sit on.
|

05-14-2018, 03:59 PM
|
 |
Member
|
|
Join Date: Oct 2011
Location: Roseburg, OR
Posts: 86
Thanks: 0
Thanked 32 Times in 17 Posts
|
|
May/June 2011
And, the assembly begins.
I spent about two hours tweaking and finessing the front cradle to be square. Doing this, you find out that factory control arms aren't perfect. Turns out the left control arm is sprung about .090 too far. I ended up getting the whole thing squared to itself within .032, and to the chassis to .032 as well.
One of the cool things about using precision water-jet cutting to make these parts is that I was able to make most of the parts self-fixturing. See the steering rack mounts below.
At this point, I started doing track-days on my SV650... this pretty much ate all of my car budget and time, so I didnt start working on it again until a few weeks ago.
By the way, does anyone from this site do car track days at Oregon Raceway? that track is amazing. very technical.
I'll post some more pics in a few.
|

05-14-2018, 04:01 PM
|
 |
Member
|
|
Join Date: Oct 2011
Location: Roseburg, OR
Posts: 86
Thanks: 0
Thanked 32 Times in 17 Posts
|
|
|

05-14-2018, 04:01 PM
|
 |
Member
|
|
Join Date: Oct 2011
Location: Roseburg, OR
Posts: 86
Thanks: 0
Thanked 32 Times in 17 Posts
|
|
|

05-14-2018, 04:03 PM
|
 |
Member
|
|
Join Date: Oct 2011
Location: Roseburg, OR
Posts: 86
Thanks: 0
Thanked 32 Times in 17 Posts
|
|
Winter 2012 Through Fall 2014
Now I needed to figure out how to connect the engine to the transmission. The OEM solution is the 'torque tube.' there are front engine mounts, a long tube that connects from the bellhousing to the transmission, and transmission rear mounts. initially, I decided not to use this since it is large, and I was worried about interior room. Also, it is too short, and getting a longer shaft that will not vibrate is tough. So, an open shaft seemed the way to go.
Unfortunately, Nobody makes an adapter that goes straight from the clutch to a driveshaft, so I had to design my own. I make castings for a living, so I figured I'd make up a pattern and have it made from aluminum.
Aligning the engine and transmission:
Cad model of the tailhousing casting
Shaft and bearing assm design
Heck I even built it!
The problem is, it is too heavy. I drove a corvette, and it already seems like the syncros had a hard time with the rotating mass of the corvette shaft, let alone mine which is 4 times heavier! At any rate, I didn't like the solution, I was concerned the mounts wouldn't keep the engine in line, and I'd have a hard time lining everything up if I ever pulled the engine. So, I decided to go back to the torque tube.
A local shop had experience lengthing these, so they did it for me. Turns out DriveShaftShop.com can make a shaft that can handle the torque and RPM just fine, so there really is no reason not to use the torque tube. It just required some diligence in making the tunnel tight to the tube, as much as possible.
With the torque tube in hand, mounting the shifter and installing the linkage went quickly, as did installing the tunnel:
Last edited by nickcornilsen; 02-19-2024 at 05:04 PM.
|

05-14-2018, 04:04 PM
|
 |
Member
|
|
Join Date: Oct 2011
Location: Roseburg, OR
Posts: 86
Thanks: 0
Thanked 32 Times in 17 Posts
|
|
Fall 2015 Through Spring 2017
More progress has been made!
With the transmission tunnel installed, I attached the upper suspension mounts:
I wish I'd taken more photos... but that's the rear suspension mocked up. Now, wheel wells begin:
I did the exhaust before I removed the transmission for working on the wheel wells, but this is a pic of it installed. It fits snug, but I can remove it all fairly easily.
Fuel cell Mount
I bought a summit fuel cell, 15 gallon with the little sump, and a gauge. To make the transmission removable, I need to be able to drop the cell out easily. Here's what I came up with, after a little Coffee and CAD:
Next, I'm going to finish mounting the fuel cell, then I'll build the straps to retain it.
Last edited by nickcornilsen; 02-19-2024 at 05:05 PM.
|

05-14-2018, 04:05 PM
|
 |
Member
|
|
Join Date: Oct 2011
Location: Roseburg, OR
Posts: 86
Thanks: 0
Thanked 32 Times in 17 Posts
|
|
Summer 2017
Here Goes again!
Between now and the last time I posted, I did manage to finish the fuel cell mounts, and even primered the back-half of the car's frame, wheel-wells, and suspension mounts. I did not, however get pictures... and I proceeded to stack parts and materials into the trunk of the car, meaning I won't be getting better pics for a while.
After primer, I got a bit distracted from the car for the summer. Barn parties, house projects, and even some track time in my Chumpcar racer stopped progress from July 15th until about 3 weeks ago.

Anyway, I've been busy though!
I decided to transition to the front of the car. There's alot of reasons for this, but mainly it comes down to poor design of my chassis jig... I can't get under the car if the floorboards are in!
The first step was working on the driver's position, pedals, and steering column.
I bought a column from a '96 camaro. I transferred the Nova columb brackets to it, and shortened it. There's enough info on how to do that out there, that I won't go into it. It's not to hard though.
I realized I was going to have to decide on an exhaust system. After some research, I decided it was either custom headers, or modify some LS7 manifolds.
LS7 manifolds are nice, the have a dual layer, and make really good power.
I purchased a pair, and cut the flanges off. You can see below, I have alot of room for the steering linkage.
The picture below shows the clutch and brake pedals installed. While trying to fit the column and pedals, I found that some of the frame tubes I'd installed back in 2012 would not work, as they took too much of my footwell. I also found out that there was no way to get an exhaust pipe through on the driver side.
Now that I'd determined the stock pedal assembly would work, and that I'd have to hack up the frame a little bit, I dove into the exhaust. You can see below what I THOUGHT I'd do for exhaust.
To prevent any extra encroachment into the passenger footwell, and to allow room for an AC evaporator, it worked best to route two 3" pipes next to eachother, and to join then under the torque tube. I set out to modify the manifolds, and re-did the frame tubes in the area to make room.
Last edited by nickcornilsen; 02-19-2024 at 05:06 PM.
|

05-14-2018, 04:06 PM
|
 |
Member
|
|
Join Date: Oct 2011
Location: Roseburg, OR
Posts: 86
Thanks: 0
Thanked 32 Times in 17 Posts
|
|
Winter 2017
Once the exhaust was done, I purchased my Vintage Air kit, test fit it, and built the passenger size footwells.
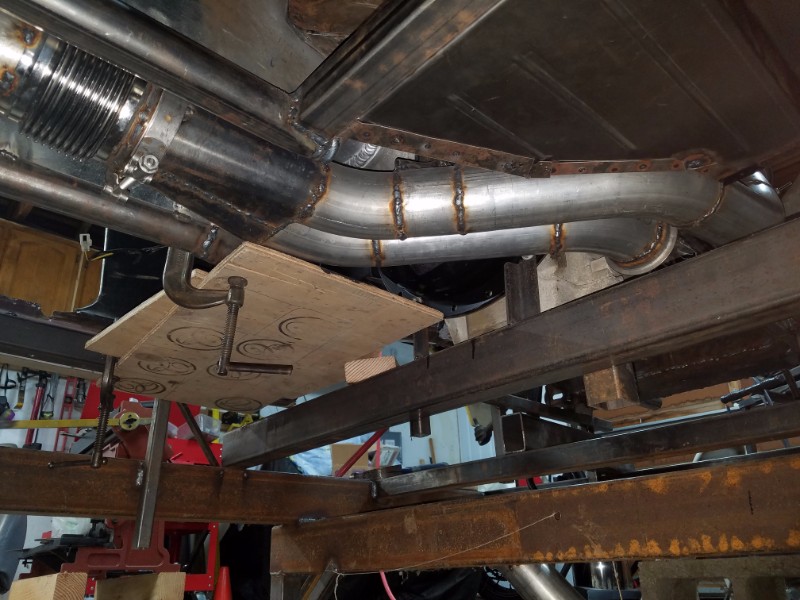 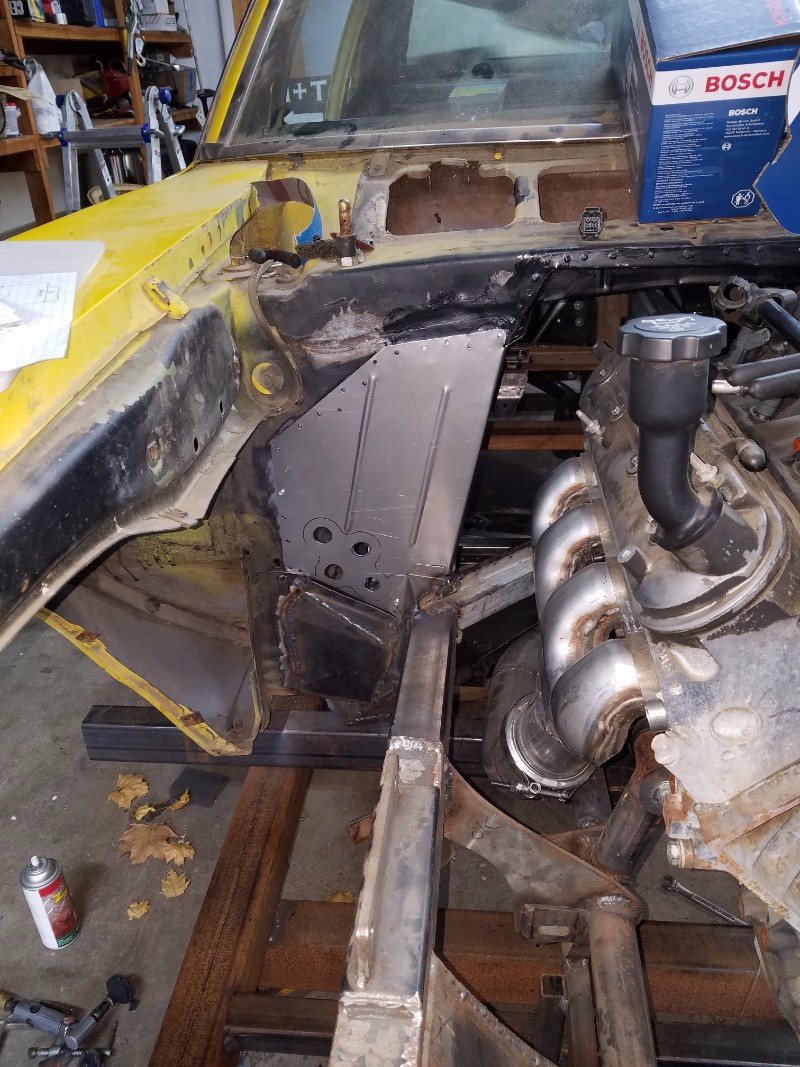
I figured i'd better check and make sure my AC kit would fit. I wanted a low mount one. It fits, quite snugly!
So, back to the pedals.
I needed to make a bracket to test the location of the gaspedal. It wasn't working to test the pedal placement without the pedals returning, so I rigged up some springs.
Now, I'm not a guy who invents the wheel when he doesn't have to. So I borrowed heavily from RomanCommander's build, and used the same bracket, booster, and clutch master he did.
|

05-14-2018, 04:07 PM
|
 |
Member
|
|
Join Date: Oct 2011
Location: Roseburg, OR
Posts: 86
Thanks: 0
Thanked 32 Times in 17 Posts
|
|
Winter 2017
More progress made!
This shows my AC unit installed under the dash, as well as the access plate for the top of the torque tube. That will be how I bleed the clutch.
Firewall Completed! This took alot of fidding, and thinking everything through. I had to buy and install the throttle cables to make that work, install the pedal assembly, and so on. I wish I didn't have to make such a patchwork, but to get everything to fit, and given my tooling limitations, I did the best I could.
3 Coats of Southern Polyurethane Epoxy!
The next phase of this project is to finish the core support, inner fenders, steering linkage, and swaybars.
Core support installed.
Motor placed, radiator just set in for reference. Lots of room for a fan! You can see the downbars, and swaybar tube mounted. the C5 bar is too wide, given that I narrowed the suspension up by 4 inches. I bought a speedway Engineering hollow tube, and pillow blocks.
|
Posting Rules
|
You may not post new threads
You may not post replies
You may not post attachments
You may not edit your posts
HTML code is Off
|
|
|
All times are GMT -5. The time now is 02:37 PM.
|