I hope my madness is welcome here. I know you guys love the growl and snarl of a badass V8 (as do I), so I am hoping this won't make you too nauseous. If numbers help any, in full race trim my electric motor will be capable of 500hp/1000ft-lb, with all 1000ft-lb available at 0rpm! Final weight goal is 1200lbs. To keep it from sounding like an electric drill on steroids, I am working on some advanced acoustic tricks, with the goal of something more like an F1 car at full boil - that's the goal anyway. More on all that later though.
The real point of this whole project was just to have a platform to display my CAD work. The compact electric powertrain gives me more freedom in design, without sacrificing performance, and opens doors for me outside the world of hot rodding. I'm really challenging myself with the design. I want it to unmistakably be a modern race car, but still look antique. For autocrossing, I chose IFS and I am going to try to make that whole setup look right - kind of like putting a Model T body on an old Ferrari grand prix chassis. Blah, blah...
What it's supposed to be (special thanks to Derek69SS for the original T pic):
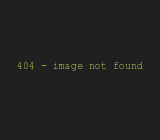
Note : don't read too seriously into the "Accused of" section - just having fun with words to play on the electric theme - I'm not a real "greenie".
I actually started this project in 2005, but got side-tracked with surviving. It originally had an SBC in it. I sold my shop in 2008 and moved to Columbus to concentrate on CAD. I left the Inhaler in storage at a so-called friend's shop for a few months. When I went back to get it, it was sitting outside in front of his shop! Anyway, this is last June, after I got it here and started working on it again. I was preparing to graft Fiero front suspension on the chassis (more on why I chose such an oddball setup later). The back is GM G-body (triangulated 4-link) snipped whole from an 83 Cutlass.
Dig the Cragar SS wheels?!

It's short for carving through cones, but the 90" wheelbase meets the NHRA minimum.
Keep going or get lost?